
Teledyne RESON A/S innså tidlig hvilken positiv innvirkning additiv produksjon hadde i deres produksjonslinje. Fra å begynne med en Stratasys uPrint Plus har nå selskapet nå oppgradert til en Fortus 380mc.
3D-printeren fikk stor betydning
Det danske selskap Teledyne RESON A/S er en av verdens ledende utvikler og leverandør av høyteknologisk sonarutstyr. De konstruerer og produserer avansert utstyr for å undersøke og kartlegge havbunnen med 3D-skanning. Kundekretsen er global og består hovedsakelig av kunder innen det maritime, forskningsinstitutt, myndigheter og militære.
Allerede i 2010 investerte Teledyne RESON A/S i en Stratasys uPrint Plus for bruk innen produktutvikling og utskrifter av prototyper. Etter 20 000 utskriftstimer ble 3D-printeren erstattet med en Fortus 380mc da selskapet innså hvilken positiv innvirkning additiv produksjon hadde i deres produksjonslinje.
Holder kostnadene nede med serieproduksjon
Ved å bruke Stratasys 3D-printer oppnår Teledyne RESON A/S besparelser i produksjonen og ungår i tillegg en stor lagerbeholdning. Det blir større rom for fleksibilitet i utviklingsfasen og ingeniørene trenger ikke lenger å tilpasse seg noen nedetid av bearbeidingsmaskiner. Med dagens 3D-printerteknologi tar det bare noen timer fra tegning til ferdig produkt.
Tanken bak investeringen av vår første 3D-printer var å få mer frihet i utviklings- og designprosessen. Vi kunne raskt konstatere at 3D-printeren ble verdifull i en mye større utstrekning i hele vår produksjonslinje. Vi har en liten serieproduksjon på 50-100 deler av avansert utstyr per år og det har vist seg å være betydelig mer lønnsomt og tidseffektivt å printe ut delene.
— Niels Stissing Jensen, ingeniør i Teledyne RESON A/S.
Ifølge Teledyne RESON A/S sparte selskapet over 260 000 kroner i løpet av de tre første årene ved å bruke 3D-printeren i egen produksjon.
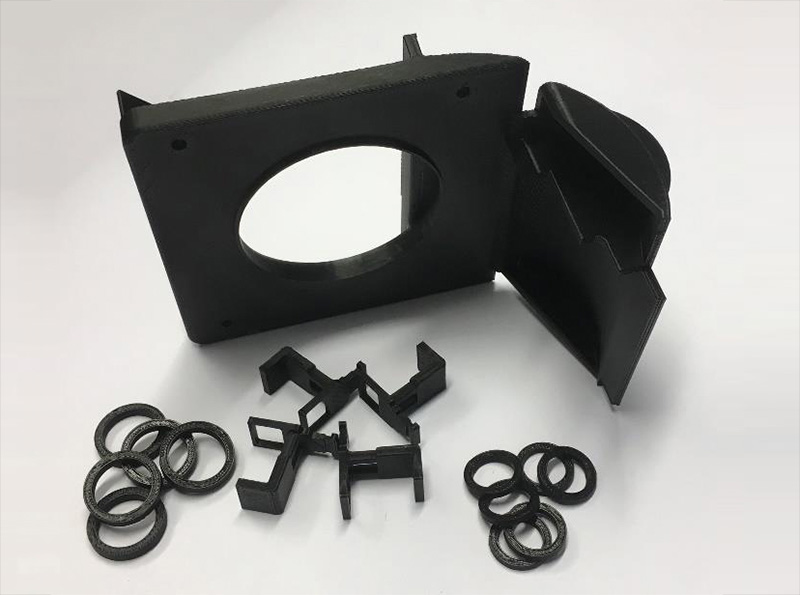

Kommer raskt videre i utviklingsfasen
3D-printeren har gjort det mulig for ingeniørene å arbeide mer fritt gjennom hele produksjonslinjen. Tidligere kunne prosjekter stoppe opp på grunn av dårlig utformede modeller og prototyper.
Tidligere så vi konstruksjonen i en 2D-tegning. Vi satt da med en håpløs geometri på en modell og ble allerede der bremset i arbeidsprosessen. I dag har vi mye større frihet i designfasen fordi vi kan printe ut en prototype på stedet og derfra raskt komme videre i utviklingsfasen. Ved et tilfelle måtte vi teste ut en konsoll på en ubåt på seks kilometers dyp. Testen kunne utføres på en dag takket være 3D-printerteknologien, noe som hadde vært helt utenkelig for noen år siden.
— Niels Stissing Jensen, ingeniør i Teledyne RESON A/S.
Med den nye Fortus 380mc kan ingeniørene printe ut flere og større modeller betydelig raskere og mer nøyaktig. Det er også et større utvalg av sterke materialer å velge mellom, avhengig av hvilke egenskaper den ferdige utskriften trenger.
Additiv produksjon som tilvirkningsmetode
Ifølge Niels Stissing Jensen finnes det ingen begrensninger innen 3D-utskriftsteknologien og han lurer på hvorfor bedrifter ikke satser mer på additiv produksjon som tilvirkningsmetode.
Jeg tror fremfor alt at en stor del av de høyteknologiske selskapene som i dag produserer mindre serieproduksjoner av nisje utstyr, kan dra nytte av å investere i en 3D-printer. Her tenker jeg på prosessen fra idé til en ferdig og funksjonell prototype som er klar til å settes i produksjon. Med 3D-printerens nøyaktighet og funksjonalitet tror jeg at det vil generere mye større fleksibilitet og plass til kreativitet i mange ulike bransjer
— Niels Stissing Jensen, ingeniør i Teledyne RESON A/S.